Vanadium carbide (VC) is a highly durable, refractory ceramic material that plays an essential role in a variety of industrial applications requiring materials that can withstand extreme conditions. Known for its remarkable hardness,wear resistance,and thermal stability, vanadium carbide is a material of choice in several sectors, including cutting tools,protective coatings,and wear-resistant components. Its exceptional strength and long-lasting performance make it ideal for high-demand processes and machinery,where material failure is not a option. In this copmrehensive product introduction,we will explore its physical and chemical properties,as well as its wide-ranging applications.
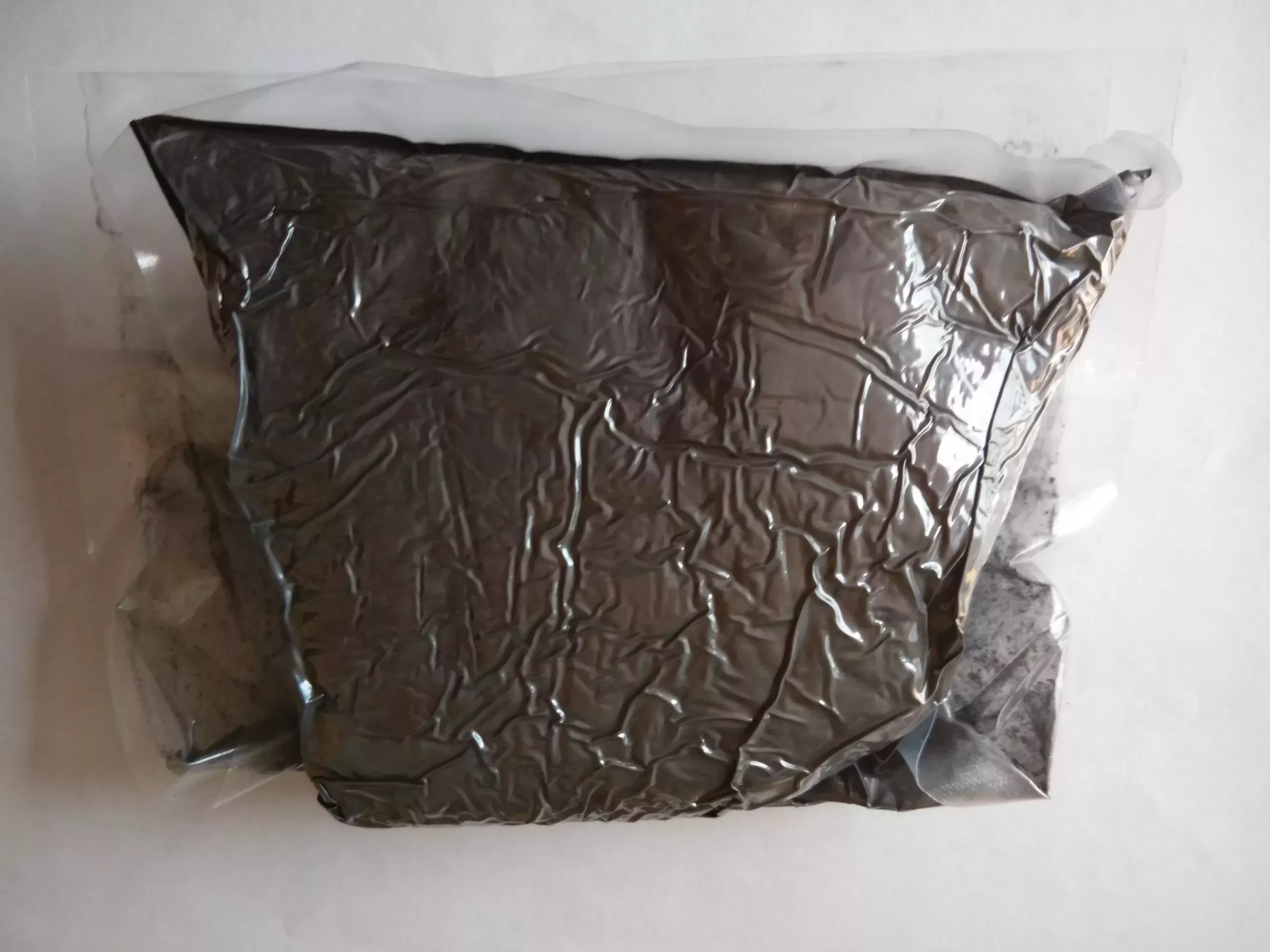
Physical and Chemical Properties of Vanadium Carbide
CAS No.:12070-10-9 | EINECS No.:235-122-5 | Molecular Formula:VC | Molecular Weight:62.95 |
Melting Point:2810℃ | Boiling Point:3900℃ | Density:5.77 | Ambient Resistance:150 |
Lattice Constant:4.182 |
Vanadium carbide is a dark gray powder,typically containing about 19.08% carbon by weight, and exhibits a cubic crystal structure (NaCl type). The compound remains stable at room temperature and pressure,making it suitable for various industrial environments. It is insoluble in cold water,hydrochloric acid,and sulfur acid,but dissolves in nitric acid and molten potassium nitrate,highlighting its chemical resistance and stability.
Vanadium carbide is commonly synthesized from vanadium pentoxide,vanadium tetrachloride,vanadium metal powder,or vanadium hydride,and plays a significant role in industries requiring durable,high-performance materials.
Applications
1.Hard Alloys and Steelmaking
Vanadium carbide powder usually works as a grain refiner in the production of hard alloys and cutting tools. It improves the physical properties of alloys by enhancing their strength,hardness,and wear resistance,thus providing greater durability and efficiency. Vanadium carbide’s ability to fine-tune the microstructure of alloys helps to enhance machining performance,making it a key material in the production of high-performance steels.
2.Cutting Tools and Machining
Vanadium carbide is especially valuable in the manufacturing of cutting tools. It is usually an additive for high-speed steel(HSS) and cemented carbide alloys, where it greatly improves the material’s hardness and resistance to wear under high-temperature conditions. In cutting tools,such as drills,end mills,taps,and inserts,VC enhances the tool’s longevity,performance,and efficiency in demanding mahcining processes.
- Hardness and Wear Resistance:VC significantly improves the hardness of tools,making them more capable of withstanding extreme cutting forces and temperatures,which are common in metalworking and manufacturing processes. The addition of VC to tool materials reduces the rate of tool wear,thereby increasing the lifespan of the cutting tool and reducing the frequency of tool replacement.
- Cutting Efficiency: VC-coated tools maintain high cutting accuracy and can sustain effective performance under heavy loads. It reduces downtime and improving overall machining efficiency. This makes VC-coated tools particularly valuable in industries such as aerospace,automotive,and metalworking,where precision is key.
3.Wear-Resistant Components
One of the standout features of vanadium carbide is its exceptional wear resistance, which makes it highly suitable for the production of wear-resistant components. VC usually applies in parts exposed to repeated mechanical stress,such as bearings, valves, seals and gears.
- Reduced Friction: VC reduces friction loss between moving parts,thereby extending the life of critical components and improving the efficiency of machinery. This characteristic is particularly important in industries such as mining,oil and gas, and heavy equipment manufacturing, where high-wear components are frequently subjected to harsh operating conditions.
- Extended Durability: With its ability to withstand harsh conditions,including abrasion,corrosion,and extreme temperatures, VC enhances the durability of wear-prone components. It reduces the need of frequent maintenance and replacements.
4.Protective Coatings
Vanadium carbide’s combination of high hardness,high melting point,and oxidation resistance. It makes it an ideal material for protective coatings on various industrial components. These coatings often get use in applications that demand high-performance materials capable of enduring extreme wear,heat and corrosion.
- Coatings for Harsh Environments: VC-based coatings apply to protect surfaces from the wear and tear caused by abrasive particles,high temperatures,and oxidative environments. This makes them invaluable in industries such as aerospace,automotive,and industrial machinery,where components are subject to extreme operational conditions.
- Corrosion and Temperature Resistance: VC coatings improve the longevity of components by protecting them from corrosion and high-temperature degradation,which is particularly crucial for parts used in heat exchangers,turbines,engines,and valves.
5.Fine Ceramics and Semiconductor Films
Vanadium carbide serves as a raw material in the production of fine ceramics and semicondcutor films. In these applications, VC typically applies in the creation of wear-resistant thin films and coatings. These films are valuable in applications requiring low friction,high durability,and stability under extreme conditions.
- Semiconductor Films: VC is a critical component in the production of semiconductor films used in electronic devices ,lithium sulfur batteries and supercapacitor devices. The excellent thermal stability and conductivity of VC make it ideal for use in semiconductor applications, where precision and reliability are crucial for microelectronics and nanoelectronics.
- Fine Ceramics: VC get use in the production of fine ceramics, which are critical in electrical insulation,optical devices,and other advanced technology applications that demand materials with high resistance to mechanical stress and thermal shock.
6.Aerospace and Automotive Industries
Vanadium carbide is particularly valuable in the aerospace and automotive industries,where its high resistance to wear,thermal shock,and oxidation. It makes it suitable for high-performance applications. In aerospace, VC is raw material for components like turbine blades,engine parts,and nozzles, where materials need to withstand high-pressure environments and extreme temperatures. Similarly,in the automotive industry,VC serves for engine components,brake discs,and cutting tools to enhance performance and fuel efficiency.
Vanadium carbide(VC) is an exceptional refractory ceramic material known for its extreme hardness,wear resistance,and thermal stability. Its properties make it indispensable across a range of industries,particularly those requiring cutting tools,protective coatings and wear-resistant components. From alloy enhancement in steelmaking to coatings for aerospace and automotive components, VC provides critical benefits in industries demanding high performance and durability under extreme conditions. Its ability to improve the lifespan,efficiency,and reliability of materials makes it a vital component in modern manufacturing, technology,and engineering.